Magnetic Flux Leakage (MFL) Inspection
CorrFlux (Ax) X2 - Magnetic Flux Leakage (MFL) Inspection
Crude oil and natural gas often contain impurities that possess inherent corrosive properties. Notably, carbon dioxide (CO2), hydrogen sulfide (H2S), and free water are prevalent in oil and gas wells and pipelines. These highly corrosive elements continuously interact with the internal surfaces of the components, leading to a gradual deterioration known as corrosion effects.
Over time, the repeated exposure to CO2, H2S, and free water causes material degradation in the lines and component fittings of the pipelines. The fluid compositions can change, wells may sour over time, and operating conditions such as pressures and temperatures can vary. These factors contribute to the loss of essential mechanical properties, including strength, ductility, and impact strength, among others. As a result, the integrity and longevity of the pipeline components are compromised, necessitating careful monitoring and maintenance to ensure safe and efficient operations.
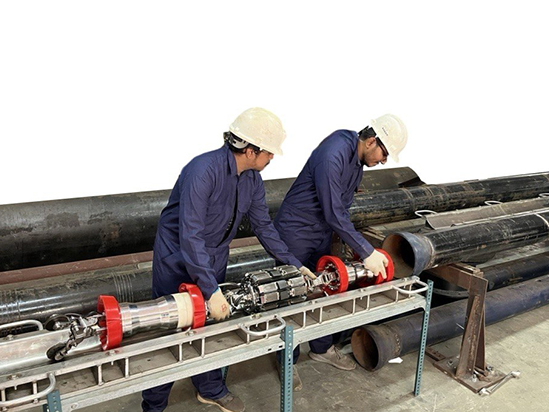
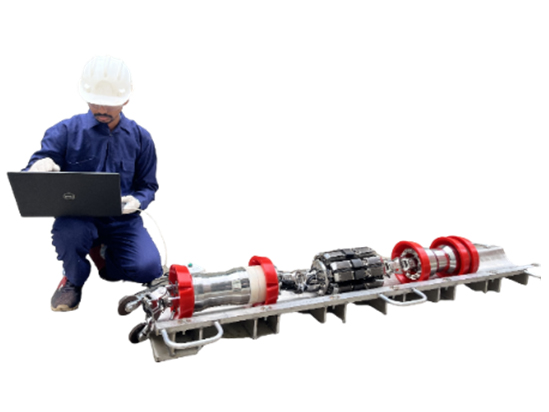
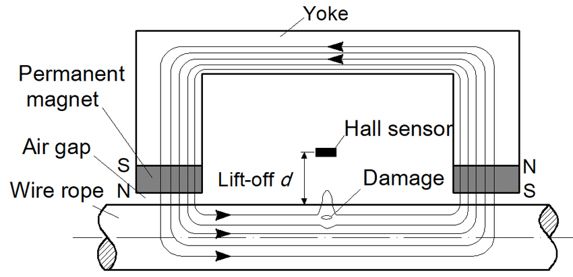
MFL (Magnetic Flux Leakage) is a non-destructive testing method that harnesses a powerful magnetic field to magnetize the steel or conductive material being examined. During this process, any anomalies or defects within the material, such as corrosion or missing metal, disrupt the magnetic field, causing it to leak out from the steel. This leakage serves as a valuable indication of the presence and location of potential flaws or imperfections in the material being inspected.
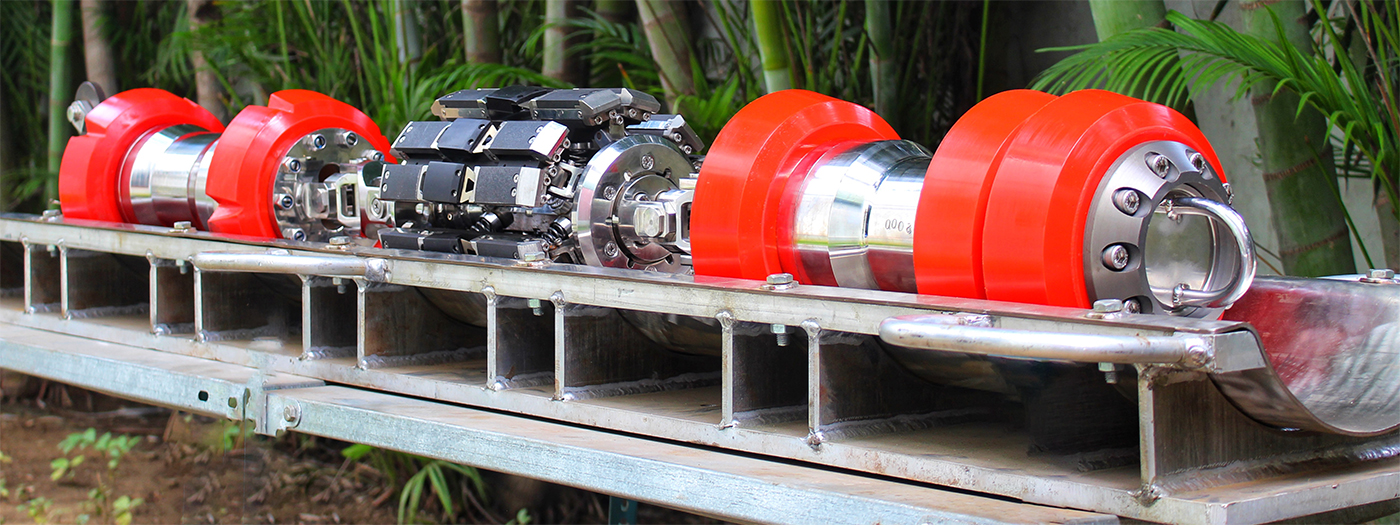
Pull Test and Loop Test
We provide the pull tests and loop tests to clients, offering an additional layer of assurance and transparency in our services.
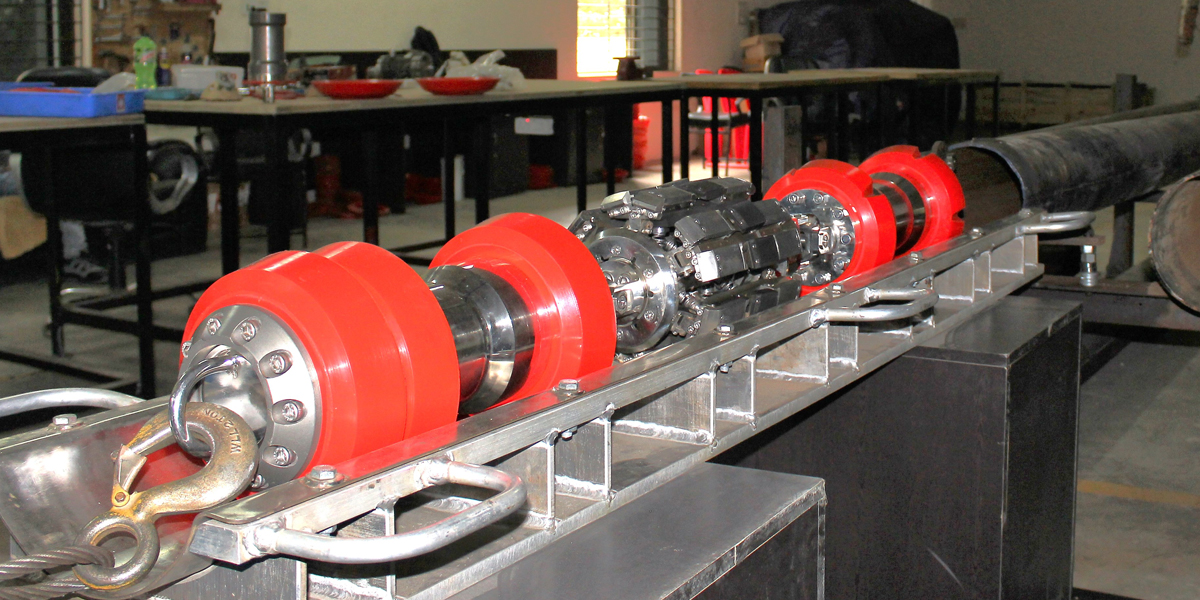
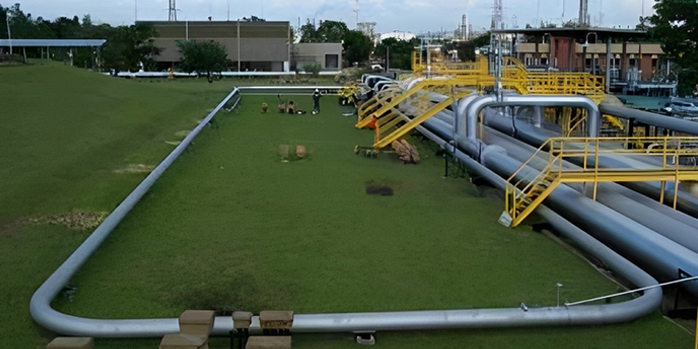
Defects in the pipeline are as POF specification and clients are invited to observe the data and software for the verification of tool performance specification.